The wonderful world of textile recycling
Maybe it is just me, because I deal with it on a daily basis, but all around me I see, read and hear about new developments in textile recycling (see also the list compiled by Circle Economy[1]). But what exactly is 'better' – mechanical or chemical textile recycling?
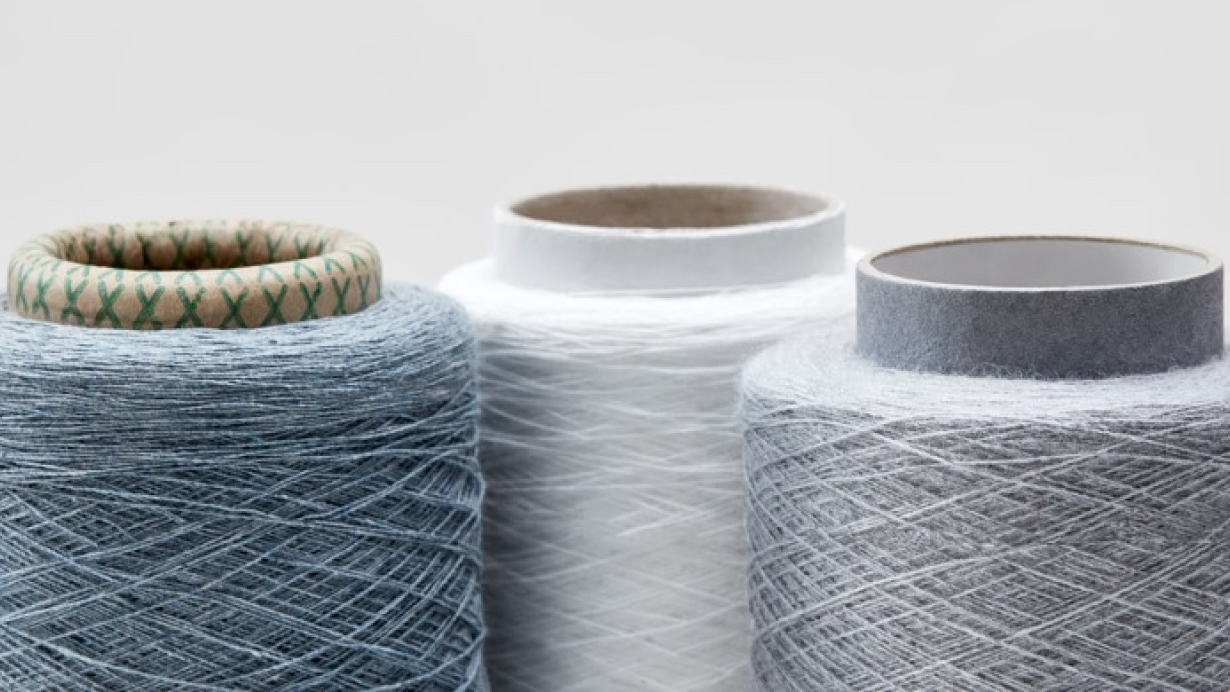
In order to answer this question, it might be useful to first briefly explain what mechanical and chemical textile recycling actually entail in broad terms. In mechanical recycling, textile waste is fiberised or melted and then spun into a new yarn. Chemical recycling involves breaking down textile waste into its smallest building blocks (at the molecular level), which are then reassembled into a textile raw material and a new yarn[1] [2]. Wolkat makes use of the mechanical recycling method mentioned first.
Both technologies have their advantages and disadvantages. For example, initiatives based on chemical recycling often focus on only one or sometimes two textile raw materials (such as cotton and polyester), whereas mechanical technology can process blends of several types of raw materials, making the mechanical process less selective in this respect. Whether a textile product is mechanically recyclable, on the other hand, depends more on the construction of a particular fabric; a knitted jumper is easier to break down into fibres than a tightly woven parka. In the case of chemical recycling, the construction of the fabric is less important.
Another difference between the two technologies is the use of colour. At Wolkat and other mechanical recycling companies, textile waste is sorted by colour, then fiberised and spun into new yarn. The recycled yarn is not dyed again, so the colour options for the new textile are fairly dependent on the source material and how it is combined into a blend. However, this method does save water and dyes. Chemical recycling, on the other hand, allows a colourful mix of coloured textile waste to be processed because the colour is filtered out during processing and then dyed again. Of course, this uses more water and dye.
The final difference between chemical and mechanical recycling is that the mechanical process makes the fibres in the yarn shorter. Which is why a certain percentage of new fibres is always added to the process to make the yarn strong enough. Chemical recycling technologies, on the other hand, generally promise to produce a fibre that is equivalent to new fibre. Whether this is really the case is still unclear. Since chemical recycling technologies are not operating on an industrial scale yet but rather on a lab scale, very little is known about the quality of the chemically recycled yarn they are able to make.
However, if you ask me, there is no contest between mechanical and chemical recycling. Both of these technologies are working hard to improve the process and, in turn, the recycled product. Similarly, Wolkat is constantly developing its processes. Both mechanical and chemical recycling have their advantages and disadvantages. The mountains of textile waste available for recycling are diverse: from a discarded sock to a broken firefighter’s suit. Some of these mountains will be better suited to chemical recycling, while others will be better suited to mechanical recycling. Both technologies are desperately needed to recycle the total amount of textile waste and create a more circular textile industry. Wolkat is therefore committed to keeping abreast of developments in the chemical recycling of textiles in order to find a viable complement to our current mechanical recycling process and to continue to recycle as much textile waste as possible.